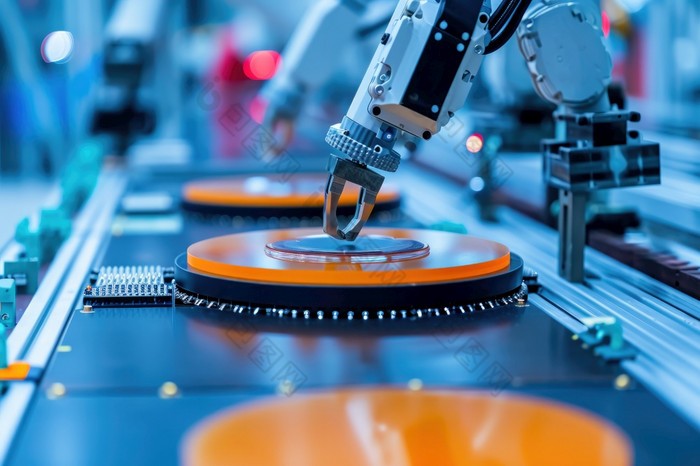
Anodizing technology, as an important metal surface treatment technology, plays a crucial role in enhancing the performance of metal materials, extending their service life, and improving their surface quality. This article will delve into the principles, process flow, application fields, as well as the advantages and disadvantages of anodizing technology.
I. Principles of Anodizing Technology
Anodizing is an electrochemical process. By placing a metal in an appropriate electrolyte and applying an external current, an oxide film is formed on the metal surface. This oxide film is mainly composed of metal oxides and possesses high hardness, excellent corrosion resistance, and good insulating properties. During the electrolysis process, metal atoms at the anode lose electrons and transform into metal ions, which enter the electrolyte. Meanwhile, oxygen ions in the electrolyte combine with the metal ions to form an oxide film on the metal surface.
II. Process Flow of Anodizing Technology
The anodizing process typically consists of three main stages: pretreatment, anodizing, and post-treatment.
1. Pretreatment: The metal workpiece undergoes processes such as degreasing, decontamination, and pickling to remove oil, rust, and impurities from the surface, ensuring the quality and adhesion of the oxide film.
2. Anodizing: The pretreated workpiece is placed in an electrolytic cell as the anode, with lead plates, graphite, etc., serving as the cathode. The power supply is then connected to initiate electrolysis. Depending on the metal material and usage requirements, suitable electrolytes and electrolysis parameters, such as voltage, current density, and electrolysis time, are selected. During the electrolysis process, a uniform and dense oxide film gradually forms on the metal surface.
3. Post-treatment: The workpiece after anodizing requires cleaning and sealing as post-treatment steps. Cleaning aims to remove residual electrolyte from the workpiece surface, while sealing involves filling the micro-pores of the oxide film through chemical or physical methods to enhance its corrosion resistance, wear resistance, and insulating properties.
III. Application Fields of Anodizing Technology
Anodizing technology is widely applied in various fields, including but not limited to the following:
1. Aerospace Industry: It is used for aircraft components, spacecraft structures, and other aviation equipment to improve the corrosion resistance and hardness of aluminum alloy components.
2. Architecture and Building Materials: It is suitable for aluminum building materials such as window frames, door frames, and curtain walls to enhance their weather resistance and surface quality.
3. Electronics Industry: It is applied to electronic device casings, heat sinks, and other aluminum electronic components to improve their heat dissipation performance and surface corrosion resistance.
4. Automotive Manufacturing: It is used for automotive components such as body structures, wheels, and engine components to enhance their corrosion resistance and hardness.
5. Medical Devices: In the biomedical field, anodizing technology can be used for the surface treatment of medical devices such as artificial joints and dental implants to improve their biocompatibility and corrosion resistance.
IV. Advantages and Disadvantages of Anodizing Technology
Advantages
1. Improved Corrosion Resistance: The oxide film can effectively isolate the metal from contact with external air, moisture, and corrosive media, significantly enhancing the metal's corrosion resistance and extending its service life.
2. Enhanced Wear Resistance: The anodized film has high hardness and wear resistance, effectively resisting wear and scratching, and improving the wear resistance of the metal surface.
3. Good Decorative Properties: By controlling the electrolysis process parameters and applying dyeing treatments, oxide films of different colors and gloss levels can be obtained, providing good decorative properties and meeting various design requirements.
4. Excellent Insulating Properties: The oxide film has certain insulating properties and can be used in electronic components and electrical equipment that require insulation.
5. Environmentally Friendly and Pollution-Free: Anodizing generally does not produce harmful gases or pollutants during the process, and wastewater can be treated to meet environmental emission standards, having a relatively small impact on the environment.
Disadvantages
1. High Cost: The anodizing process requires specialized equipment and electrolytes, resulting in significant equipment investment. Additionally, the electrolysis process consumes a large amount of electrical energy, leading to relatively high production costs. Moreover, the process is complex, involving multiple steps such as pretreatment, anodizing, and post-treatment, which also increases labor costs.
2. Limited Effectiveness for Complex-Shaped Workpieces: For workpieces with complex shapes, deep holes, blind holes, or internal structures, it is difficult to ensure the uniformity of the anodized film. Problems such as uneven film thickness, local lack of film, or poor film quality may occur, affecting the treatment effect and product performance.
3. Low Production Efficiency: The anodizing process usually takes a long time, especially for workpieces requiring a thick film thickness, where the electrolysis time may last for several hours or even tens of hours. This results in low production efficiency and is not suitable for large-scale, high-efficiency production needs.
4. Porosity of the Film Layer: Despite the ability to reduce porosity through sealing treatments, the anodized film still has certain micro-pores. This may allow corrosive substances to penetrate through the micro-pores to the metal substrate surface in special environments, such as high temperature, high humidity, or strong corrosive media, reducing the protective performance of the film layer.
5. Material Limitations: Anodizing is mainly applicable to a few metals and their alloys, such as aluminum, magnesium, and titanium. For other metal materials, such as steel and copper, the anodizing effect is not ideal or requires special processes and electrolytes, limiting its application range.
V. Conclusion
Anodizing technology, as an important metal surface treatment technology, has significant advantages in enhancing the performance of metal materials, extending their service life, and improving their surface quality. However, issues such as high cost, limited effectiveness for complex-shaped workpieces, low production efficiency, and film layer porosity still require further research and improvement. In the future, with the continuous development of materials science and surface engineering technologies, anodizing technology is expected to be applied and promoted in more fields.
AMTD provides high-precision Showerhead services for core components. Its products mainly include semiconductor equipment core components such as Shower head, Face plate, Blocker Plate, Top Plate, Shield, Liner, pumping ring, and Edge Ring. These products are widely used in fields such as semiconductors and display panels, with excellent performance and high market recognition.
Information Sources: The information in this article is mainly sourced from authoritative channels such as WeChat Official Accounts (Tencent), Zhihu Columns, and Hardness Depth Testing.
上一篇:21 Surface Treatment Technologies
下一篇:Common Machining Processes